You Can’t Teach A New Dog Old Tricks: Using Tech To Bridge Crucial Safety Knowledge Gaps
The great resignation is an ongoing phenomenon that’s been affecting firms across all verticals since 2021. As of July 2023, the US Bureau of Labour Statistics recorded over 4 million monthly voluntary resignations across the US, compared to a rate of 3 million 5 years ago. This mass exodus has major implications across a firm’s functions and has caused headaches from the boardroom to frontline operations. For organizations with prominent safety hazards, the loss of experienced heads has left operational teams exposed to a higher risk profile. Following the lead of other business areas, EHS decision-makers must explore digital investment opportunities to bridge the knowledge gap and mitigate the risk of inexperience.
When bridging the safety competency gap, EHS leaders shouldn’t divert all focus onto catastrophic risks – more common injuries can also have immense cumulative consequences. Take work-related musculoskeletal injuries, which are the cause of 7.3 million lost working days annually in the UK, according to the HSE’s 2022 report. For firms in labour-intensive industries, improper technique can lead to life-altering injuries. AI is central to effective digital ergonomic solutions, with providers Intenseye and VelocityEHS using computer vision to perform musculoskeletal risk assessments on employees.
Employee inexperience is highlighted in intricate, higher-risk tasks. Firms typically deploy control of work (CoW) processes to mitigate the hazards of such tasks. Historically, CoW was paper-based, included numerous steps, and entailed significant back and forth between operators and safety supervisors. Over the last three years, we have witnessed heavy investment in digitally enabled CoW solutions across numerous industries (see Verdantix Buyer’s Guide: Control of Work Software Applications.) Digital CoW tools help to guide inexperienced operators through necessary precautionary workflows, such as job hazard analysis and asset isolations, to efficiently check that appropriate risk controls are in place. For example, Intelex and Sphera integrate CoW with training to offer just-in-time microlearning refreshers, while Aveva uses digital twin visualization of complex assets to ensure lock-out-tag-out procedures are carried out accurately.
Often ‘at one’ with the site they manage, experienced employees in process industries are invaluable resources: their sixth sense for spotting potential hazards plays a prominent role in hazard control. When employees of this calibre retire or leave, firms can turn to digital tools to recognize and respond to high-risk situations. Risk visualization has been a top investment area for process safety management software vendors (see Verdantix Best Practices: Moving EHS To Dynamic Risk Management). Take Enablon, which displays outputs of its risk engine through dynamic barrier and bowtie risk diagrams to give a real-time picture of hazards and controls surrounding a task or asset. Alternatively, witness GOARC’s emergency response solution, which compiles real-time data to accurately manage hazard mitigation responses. This is a vital resource to react to process safety incidents, and also helps to hone employee competency during training drills.
To view more Verdantix research, visit the website here.About The Author
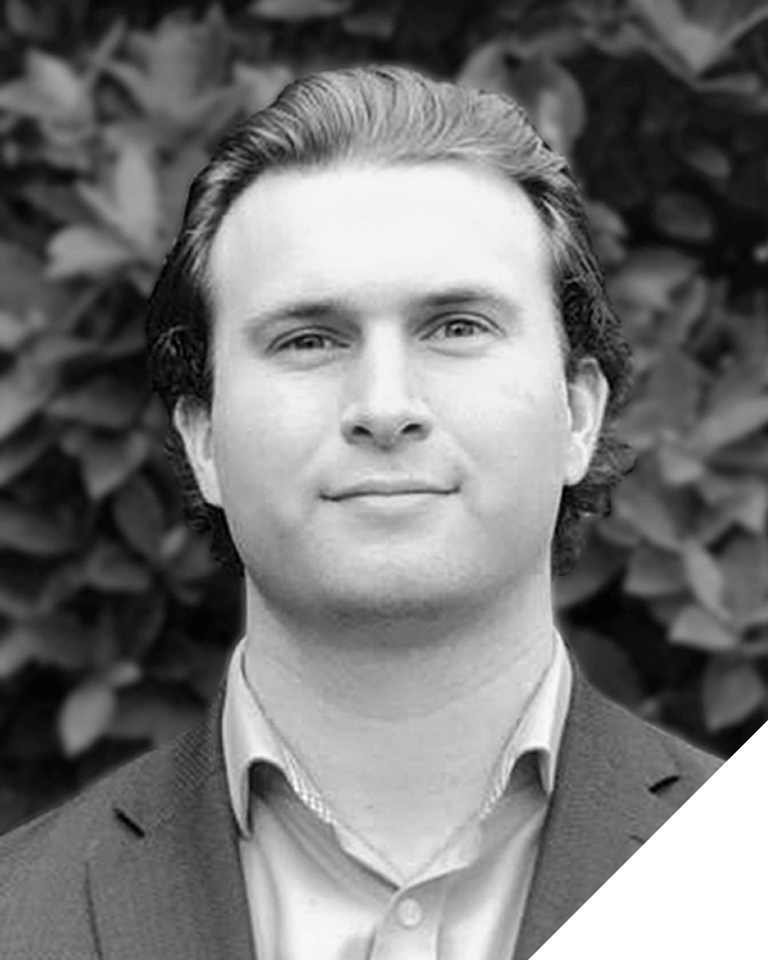
Tom Brown
Senior Consultant, Advisory Services