An Essential Guide To Predictive Maintenance
Imagine a world where asset managers no longer had to rely on gut feelings, outdated records and complicated excel sheets to make business critical decisions. Trade-off situations between maximizing the useful life of an asset at the risk of failure and maximizing uptime through early replacements could be optimized with data-driven insights and automated actions.
Well, operations and maintenance managers can use predictive maintenance solutions to streamline decision-making, resulting in increased asset reliability and performance. While predictive maintenance is not a new concept, the significant rise in industrial Internet of Things (IIoT) sensors, data-driven analytics, and vendors entering this space, mean that such solutions are now more accessible to firms of all sizes and maturity than ever before.
According to the recent Verdantix operational excellence global corporate survey, out of the 301 executives interviewed, nearly a fifth of those are planning new investment in commercial asset failure prediction software in 2023.
While transitioning to predictive maintenance may be on your firm’s agenda, understanding where to start and how to actually implement a solution is a whole different challenge. While the steps may vary depending on objectives, industry, and asset types, Verdantix has outlined best practices for moving from a reactive to proactive and predictive maintenance strategy:
- Understand criticality of assets and any data gaps that exist – Predictive maintenance is most effective from an operational and cost perspective when applied to the most critical assets. Firms should work with service providers or vendors such as Itus Digital and Pragma to understand which assets are most critical and if there is sufficient sensors and data available to effectively predict asset health and performance.
- Select predictive maintenance software provider – Firms should assess vendor solutions based on their industry expertise, success stories, ease of integration with existing portfolio and the implementation and training support provided. In the Verdantix Green Quadrant for APM software, AspenTech, AVEVA, Bentley Systems and GE Digital scored the highest for their asset failure prediction capability.
- Create a digital twin ecosystem to enhance predictive maintenance – Firms should consider combining analytical data from predictive maintenance solutions with simulations and visualizations to create a digital twin, that enable firms fully optimize asset performance. In the global survey 84% of respondents stated that reducing asset downtime through predictive analytics as an important value propositions offered by digital twins for industrial facilities.
- Revaluate maintenance strategies on an ongoing basis - Developing an optimal maintenance strategy is an ongoing process, which requires updating based on insights from asset failures and subsequent lessons learned. Firms should ensure a continuous cycle to improve maintenance strategies with respect to changing business demands is in place. Baker Hughes offers simulation-based maintenance task optimization capabilities to analyse different maintenance regimes.
- Scale and expand strategies to include more assets and sustainability KPI’s – Predictive maintenance strategies not only reduce maintenance costs and downtime but also improves energy consumption and monitoring. Firms should scale deployments across similar asset types, promoting all types of benefits to ensure enterprise level buy in.
For more information on predictive maintenance technologies and the software market dynamics, please read Verdantix Green Quadrant: Asset Performance Management Solutions 2022, Verdantix Product Benchmark: Predictive Maintenance Functionality Of APM Software and Verdantix Best Practices: Transitioning To Predictive Maintenance For Enhanced Asset Management.
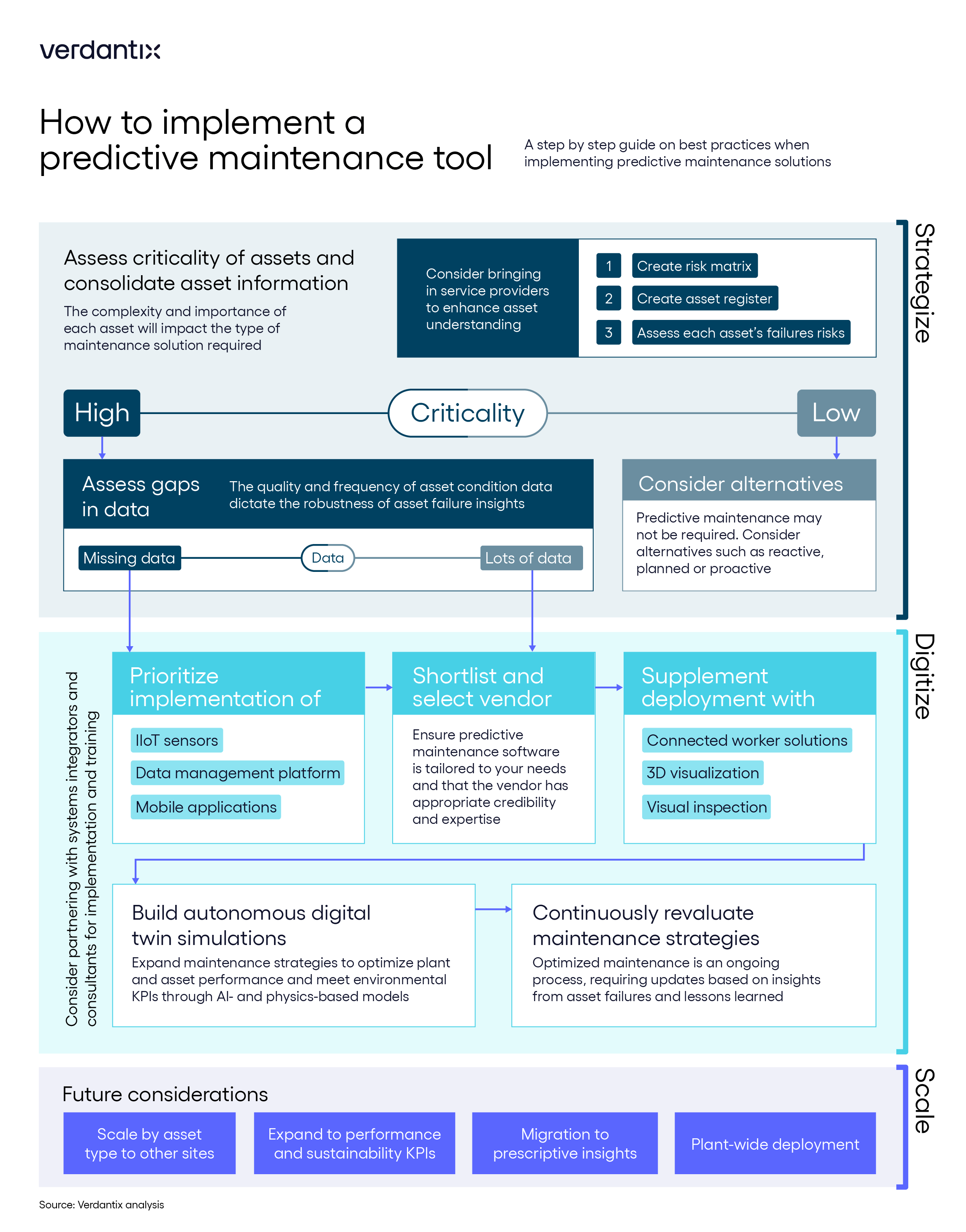
About The Author
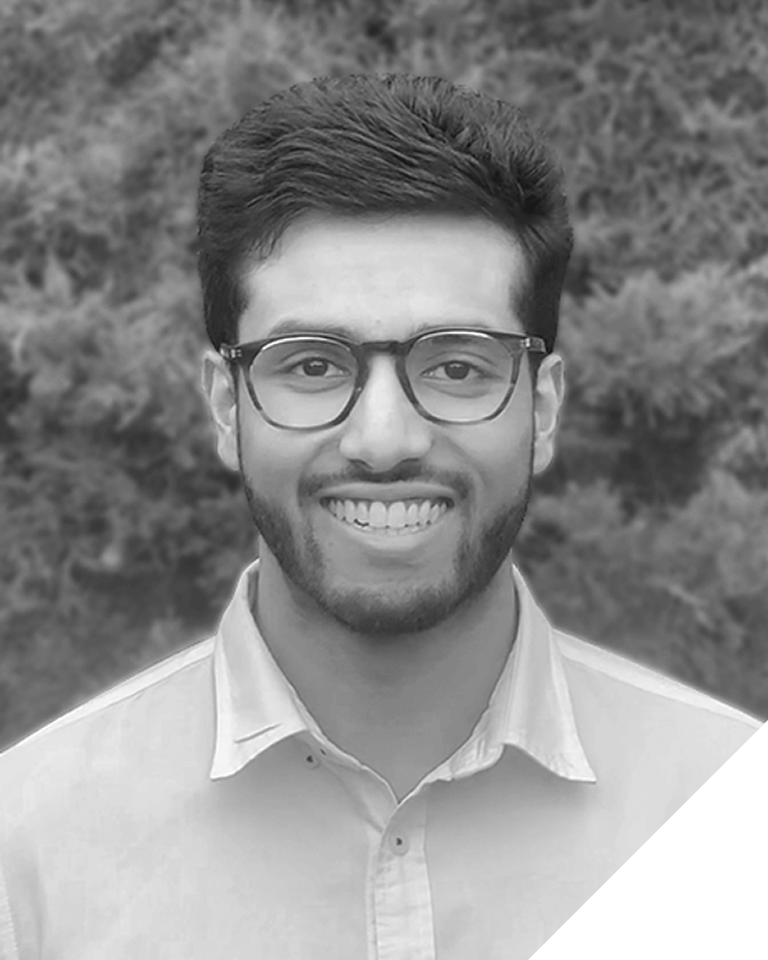
Kiran Darmasseelane
Principal Analyst