Transforming Apparel Manufacturing: Embracing A Circular Economy With 3D Technology
The apparel industry is one of the most resource-intensive sectors in the world: annually, 92 million tonnes of textile waste are generated globally. In the US alone, around 85% of all textiles thrown away – about 13 million tonnes – are either sent to landfill or incinerated. Consequently, the industry faces rising pressure to address its climate impact as a top contributor to GHG emissions, water pollution and landfill waste. As the sector looks to tackle this, 3D technology for fashion is an innovative solution that holds significant potential, for both business and the environment.
Recent advances and adoption of 3D technology
Over the last five years, 3D technologies such as printing, weaving and knitting have seen a significant influx of funding and uptake. In August 2024, for example, 3D weaving technology provider unspun raised $32 million in a Series B funding round led by deep tech investor DCVC, and has already signed multi-year agreements with retailers like Walmart to deploy its Vega machines for localized production in both North America and Europe. Brands are increasingly leveraging 3D technology to produce items, with examples such as:
- Italian multinational group Legor is now using 3D technology to create jewellery and fashion accessories made from 100% precious metals from recycled sources, advancing its objectives of fostering a circular economy.
- Various members of the fashion industry are using advanced polymer materials to create intricate patterns and structures that were previously impossible with traditional methods.
- Some of the biggest names in footwear and fashion — Adidas, Dior, Fendi, New Balance, Nike, Reebok – have leveraged the technology with substantial benefits. Using 3D printing for prototyping and to produce customized athletic shoes has reduced Nike’s development cycle by 50%, allowing quicker go-to-market models and response to market trends.
Regulatory support
We are witnessing rising demand for sustainable products. The EU, for example, has implemented the Ecodesign for Sustainable Products Regulation, which mandates energy efficiency and environmental considerations in textile manufacturing. Similarly, in the US, the Consumer Product Safety Commission (CPSC) has issued guidelines for 3D printed textile products, focusing on the safety of materials used – especially for wearable items.
Towards circular manufacturing
3D technology minimizes waste and emissions and enables circular production for the apparel sector. According to unspun, its Vega technology allows traditional cut-make-trim facilities to make clothing four times faster, with 53% emissions reduction, 49% reduced energy demand and a 39% reduction in blue water consumption – and less than 3% waste of cut fabric compared with the industry average of 15%. The business value extends beyond sustainability, as the technology lowers production costs, accelerates time-to-market and enhances design capabilities. As regulatory frameworks evolve and more firms embrace this technology, the potential for growth and positive environmental impact is immense.
To learn more about 3D technology and its role in the circular economy, look out for our upcoming Tech Roadmap and read the following reports:
Strategic Focus: Redefining The Role Of Remanufacturing In The Circular Economy Through Innovation
About The Author
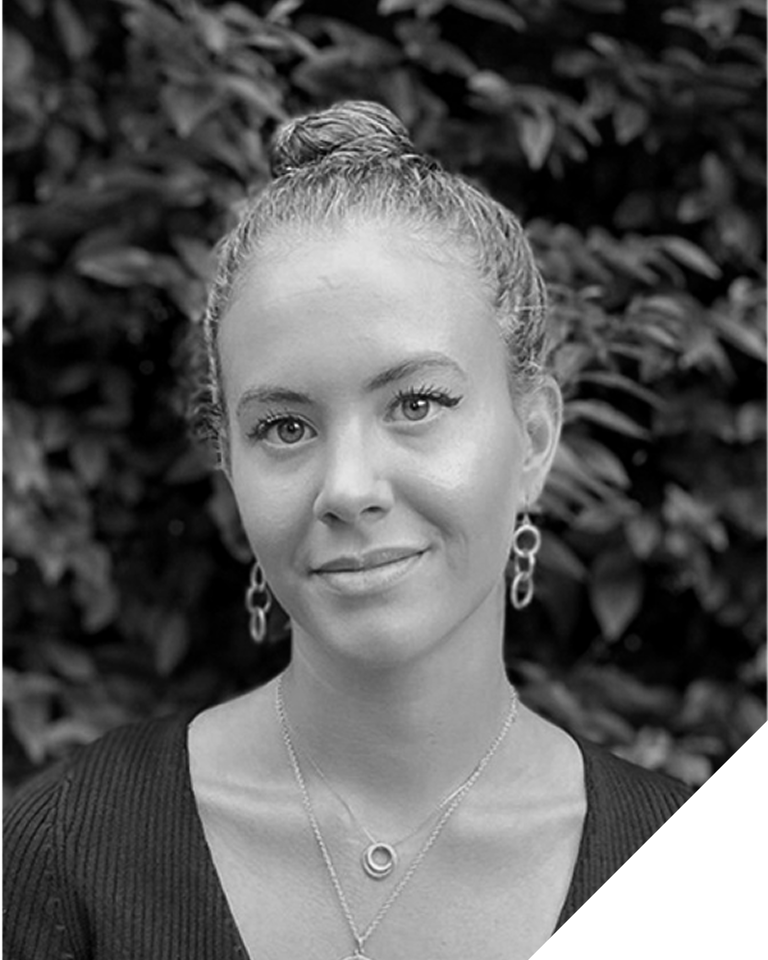
Jessie Wilson
Industry Analyst