Three Technologies Delivering Industrial Energy Efficiency
Running an industrial plant where machinery operates reliably, processes stay optimized and energy is used efficiently sounds like an industrial dream. But with today's technological advancements, that dream is increasingly becoming a reality. Modern software tools are helping industrial organizations reduce energy waste, boost performance as well as quality and meet sustainability goals in tangible ways. Among the most impactful solutions are predictive maintenance systems, process optimization tools and comprehensive energy management platforms – each offers a unique path toward more intelligent and efficient operations. Responses to the 2025 Verdantix global corporate survey of industrial transformation decision-makers indicate that firms expect to increase spend on these software categories in 2025. Here’s a breakdown of exactly what these three innovative technologies entail and what benefits each has to offer:
- Staying ahead with predictive maintenance.
Unexpected machine failures can derail production, drive up energy use and lead to costly repairs. Predictive maintenance software is designed to prevent that disruption. By combining IIoT sensors with advanced AI analytics, industrial firms can monitor machinery in real time and detect issues before they escalate and become more costly to remedy. Nanoprecise’s predictive asset maintenance and machine health monitoring solutions, for instance, use smart sensors to track subtle changes like temperature fluctuations and vibrations – early signals that help maintenance teams act before efficiency drops or expensive breakdowns occur. With smoother operations and fewer surprises, energy is used more effectively and downtime is minimized, making predictive, energy-centred maintenance a smart – and in many cases essential – investment for energy-conscious industries.
- Unlocking hidden savings with process optimization.
Inefficiencies in industrial processes often go unnoticed until they start affecting output or inflating energy bills. Process optimization software helps uncover these blind spots by analysing operational data continuously and making real-time adjustments. For example, QiO Technologies’ Foresight Platform leverages analytics to identify where adjustments can be made to reduce waste and improve performance, offering actionable insights that help teams finetune their operations. The result is not only energy savings and consistent productivity, but also better overall control of day-to-day operations. Businesses adopting process optimization tools often report reduced energy costs and lower emissions, finding that incremental improvements add up quickly and deliver tangible economic benefit. By continuously monitoring process metrics like natural gas use in heavy industries and adjusting flow in accordance with historical and real-time data, industrial organizations benefit from greener operations and lower energy costs. Unsurprisingly, a staggering 75% of global corporate survey respondents indicate that their firm plans to increase spend on production and yield optimization, with 44% stating that they expect a double-digit increase.
- Seeing the bigger picture with energy management.
To manage energy well, businesses need a clear view of how it's being used across their facilities. Energy management software provides that visibility, helping teams make informed decisions quickly and confidently. Tools like Siemens’s SIMATIC Energy Management Software deliver intuitive dashboards and detailed analytics that make it easier to track consumption patterns, identify inefficiencies and prioritize improvements. Additionally, the provider’s SIMATIC Energy Manager enables organization-wide energy management, linking energy and production data, and subsequently assisting industrial firms in getting a better understanding of the efficiency of their operations. With TÜV German Technical Inspectorate certification, SIMATIC Energy Manager facilitates compliance with the statutory regulations required by ISO 50001 while simultaneously enabling plant operations to be both energy- and cost-efficient.
To learn more about effective approaches driving industrial energy efficiency, check out:
- Market Insight: Firms Invest In Industrial Software For Net Zero Strategies
- Global Corporate Survey 2025: Industrial Transformation Budgets, Priorities And Tech Preferences
About The Author
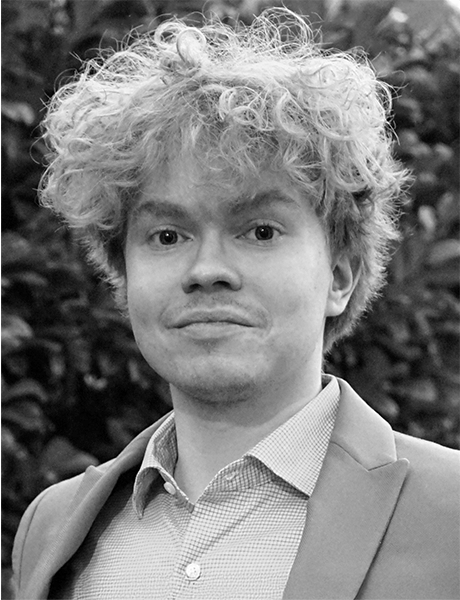
Robin Sureda-Tasis
Analyst