Seeing The Forest And The Trees: Five Best Practices For Successful Industrial Digital Twins Implementation
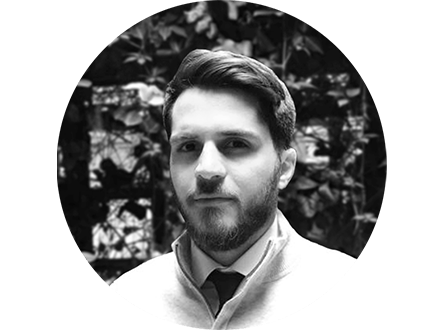
Victor Voulgaropoulos
Digital twin projects can be seen as the pinnacle of digital transformation journeys and, if done well, culminate in cross-functional enterprise value. Driven by operational excellence initiatives, cost-cutting programmes and COVID-19 crisis concerns, the digital twin market for industrial facilities is expected to triple over the next five years at a CAGR of 24%.
Despite this uptake, 74% of 259 senior execs in industrial organizations interviewed in our recent global corporate survey reported that they perceive digital twins as being complex projects. While there is no one-size-fits-all approach for implementing digital twins in industrial facilities, vendors and clients need to think of the projects both tactically and strategically. Project managers cannot view the challenges posed by digital twins as one-off events; instead, they should establish processes to ensure sustained excellence and thus value from such projects – achieving both short-term results but also facilitating long-term objectives.
Apart from selecting the right vendor, or indeed partner, for this digital twin journey, organizations must also tackle five internal challenges during the implementation:
#1 Driving enthusiasm with leadership and end-users
Organizations should communicate the digital twin benefits across stakeholder groups to garner enthusiasm, drive support both from senior leadership and end-users, and build well-founded change management processes to facilitate sustained returns.
#2 Developing robust data governance and operations
Implementations will fail without a robust data strategy; digital twins require comprehensive data governance programmes and DataOps capabilities as well as good understanding of ‘dark’ data-related risks; software platforms such as Bentley Systems AssetWise, Cognite CDF and Uptake Fusion can enable and accelerate such efforts.
#3 Identifying and resolving instrumentation gaps
Sensors and actuators, the backbones of dynamic digital twins, need to be installed strategically to help the twin optimize real plant performance. However, in high-risk industries such as mining, sensor failures are commonplace; Newcrest, leveraged OSIsoft’s (now part of AVEVA) ML-powered ‘soft sensor’ application instead, reducing downtime by 50% and increasing throughput by 650,000 tonnes within six months while avoiding the costly hardware replacements.
#4 Ensuring reliable connectivity across the network
Choosing the right communication protocols and network platforms is pertinent to allowing dynamic and smooth operations without bandwidth issues and enough computational power. When designing or upgrading the network, plant managers should consider network connectivity, IoT gateways, device management, industrial software support, network security and data orchestration.
#5 Fortifying the plant’s IT security
Cybersecurity is paramount for minimizing exposure to vulnerabilities such as data being compromised, and organizations must strike the right balance between pragmatism and safety. Building auditable authentication systems to monitor data trails, ensuring the right level of user access, asking technology providers for ISO certifications, and having a black swan and critical event management software platform such as the one from Everbridge, can substantially minimize IT incident response time and disruption.
To learn more about the best practices around implementing digital twins, read the new Best Practices: Implementing Industrial Digital Twins report or get in touch at [email protected].
About The Author
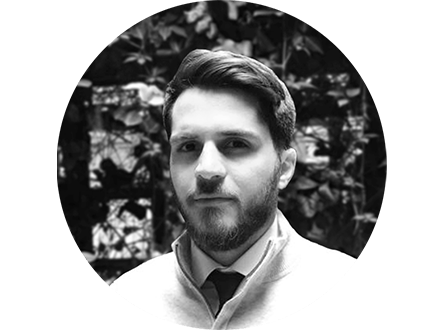
Victor Voulgaropoulos
Senior Analyst