Navigating The Digital Twin World: Finding Your Perfect Match
The demand for digital twins – virtual replicas of real-world assets used to improve plant operations — has been prevalent for a number of years. So much so that nearly three-fifths (59%) of the 301 executives interviewed in the Verdantix 2022 global survey have implemented, are implementing or plan to implement digital twins in the next 12 months. Additionally, eight out of the nine value propositions offered by digital twins were valued as ‘important’ or ‘very important’ for industrial facilities by over 80% of respondents.
However, a digital twin is not a monolithic application. It represents the alignment of varied data types, such as asset- and plant-specific information, with analytics, simulation and 3D visualization. Therefore, when it comes to choosing a digital twin solution, it's crucial to understand your organization’s goals and requirements. Some offerings are best suited for simulation and visualization, while others are more focused on data analytics and prediction. It's important to evaluate the value proposition of a digital twin to ensure it aligns with your specific needs. Key value propositions include:
- Holistic risk visualization and streamlined data management, as offered by descriptive or informative digital twins. Users can expect to gain an improved understanding of assets and a single source of truth for all data based on existing IT infrastructure. Such models offer an easy-to-use interface to visualize design and operational data, enhancing existing processes without disrupting work routines. In collaboration with strategic partners Aize and Cognite, Aker BP is developing a digital twin to help operations better manage data in addition to creating a safer workplace, increasing production, and lowering costs and emissions.
- Reduced asset downtime and production optimization, achieved by leveraging analytics for advanced and predictive asset performance maintenance strategies. Predictive digital twins visualize asset health in real time, perform ‘what if’ studies and propose remedies to avoid unplanned events. The digital twin supports the optimization of maintenance, engineering and operational decisions. Using GE Digital’s APM suite to create a digital twin, wind energy producer EDP Renewables gained real-time alerts, early warning notifications and asset performance predictions to reduce unplanned downtime and improve asset utilization.
- Streamlined product development and operator training. Combining physics-based principles and machine learning capabilities in the form of an autonomous digital twin allows firms to simulate and optimize the entire asset life cycle from design through to engineering and operations. The twin creates a highly accurate data model that dramatically reduces the number of experiments required at R&D phases, and provides realistic operator training simulations and real-time insights to combat demand and energy consumption challenges. Aspen Technology has created its Aspen Hybrid Models, which embed industrial AI in its Aspen Plus and Aspen HYSYS process simulators, to create models to improve plant performance. A global refinery expects that deployment of the Aspen Hybrid Models at its 200,000-barrel-per-day operation will enable it to better manage changes in required production volume, delivering value of more than $10 million annually.
When choosing a digital twin solution, it's important to consider factors such as integration, scalability, support, customization, security, and cost. By taking the time to find the right fit, you can ensure that your digital twin investment delivers the benefits you expect and supports your business's growth.
To learn more about autonomous digital twins and the significance of physics-based models, look out for the upcoming Verdantix report – Strategic Focus: High Value Use Cases And Benefits Of Operationalizing Digital Twins With Process Simulations.
About The Author
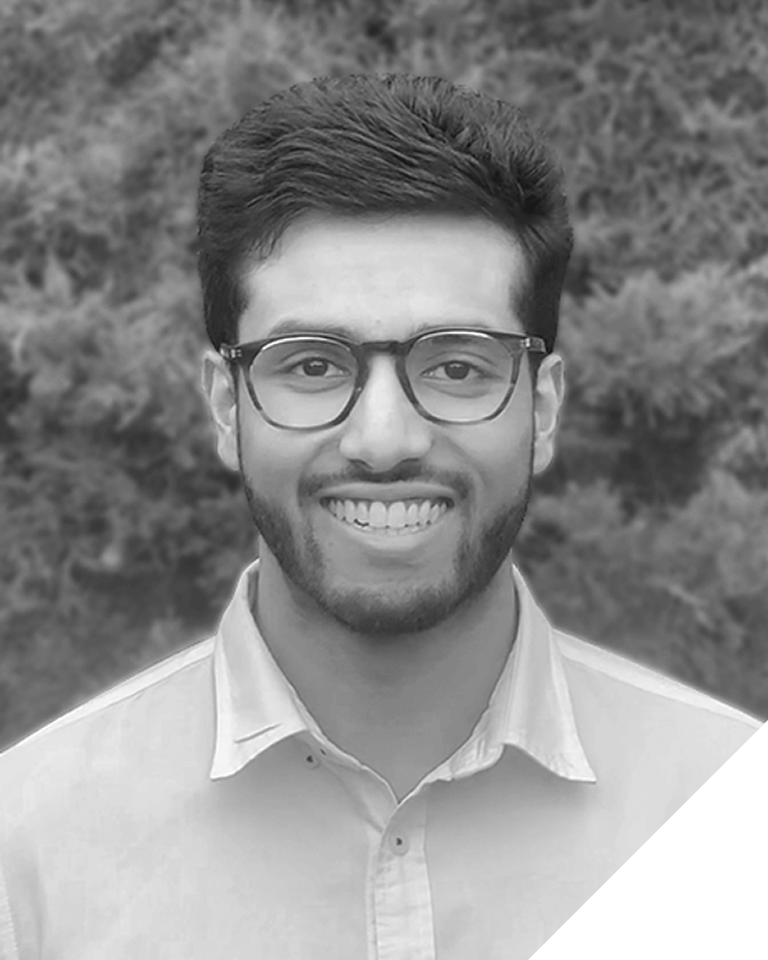
Kiran Darmasseelane
Principal Analyst