Digital Twins As A Catalyst For Achieving ESG And Sustainability Objectives
13 Jun, 2022
Digital twin technology is emerging as an innovative tool for companies to help hit their ESG and sustainability goals. Firms in oil and gas and to a lesser extent within mining and power utilities are rapidly implementing digital twins to achieve their net zero and energy transition objectives because these markets have a high level of environmental impact; therefore, some of the most regulated.
Earlier this year GE Digital released its Autonomous Tuning Software for gas turbines that creates a digital twin model of the gas turbine to find optimal flame temperature and fuel splits. The autonomous tuning software senses environmental and physical degradation changes in real-time to allow for automatic adjustments to ensure the gas turbines run efficiently at low emissions and acoustic levels. What-if simulations can be undertaken with digital twins to optimize production and asset performance and lower emissions level that way as well. In March, Microsoft announced a digital twin project for the mining industry through a partnership with Newcrest. The technology uses real time operational data to generate a 3D visualization of the mining process to improve performance and lower emissions. A sustainability focused data model for ESG reporting will be released this month.
Predictive analytics and what-if simulations will be the most common ways digital twin is used for sustainability because these applications are the most impactful to company operations. In our 2021 global corporate survey 76% of the 256 respondents stated reducing asset downtime through predictive analytics or optimizing production efficiency through what-simulations provided the highest value proposition to them. However, these aren’t the only digital twin applications that can improve ESG and sustainability for firms. Implementing digital twins to ensure worker or plant safety with holistic risk visualization or staff training with accurate simulations lowers the risk of accidents and incidents both on people as well as the environment. Shell’s Nyhamna gas plant was able to improve the risk assessment of all activities by integrating its systems and data in Kongsberg’s Kognitwin platform. This allowed the Nyhamna gas plant to step closer towards achieving zero incidents or leaks. Another example is soft sensor modeling to improve production quality. A more efficient manufacturing process contributes to optimal usage of all materials involved along with controlled emission levels.
For more information on industrial digital twins read the following Verdantix reports: Smart Innovators: Digital Twins For Industrial Facilities; Best Practices: Implementing Industrial Digital Twins; Market Size And Forecast: Digital Twins For Industrial Facilities 2021-2026 Global
Earlier this year GE Digital released its Autonomous Tuning Software for gas turbines that creates a digital twin model of the gas turbine to find optimal flame temperature and fuel splits. The autonomous tuning software senses environmental and physical degradation changes in real-time to allow for automatic adjustments to ensure the gas turbines run efficiently at low emissions and acoustic levels. What-if simulations can be undertaken with digital twins to optimize production and asset performance and lower emissions level that way as well. In March, Microsoft announced a digital twin project for the mining industry through a partnership with Newcrest. The technology uses real time operational data to generate a 3D visualization of the mining process to improve performance and lower emissions. A sustainability focused data model for ESG reporting will be released this month.
Predictive analytics and what-if simulations will be the most common ways digital twin is used for sustainability because these applications are the most impactful to company operations. In our 2021 global corporate survey 76% of the 256 respondents stated reducing asset downtime through predictive analytics or optimizing production efficiency through what-simulations provided the highest value proposition to them. However, these aren’t the only digital twin applications that can improve ESG and sustainability for firms. Implementing digital twins to ensure worker or plant safety with holistic risk visualization or staff training with accurate simulations lowers the risk of accidents and incidents both on people as well as the environment. Shell’s Nyhamna gas plant was able to improve the risk assessment of all activities by integrating its systems and data in Kongsberg’s Kognitwin platform. This allowed the Nyhamna gas plant to step closer towards achieving zero incidents or leaks. Another example is soft sensor modeling to improve production quality. A more efficient manufacturing process contributes to optimal usage of all materials involved along with controlled emission levels.
For more information on industrial digital twins read the following Verdantix reports: Smart Innovators: Digital Twins For Industrial Facilities; Best Practices: Implementing Industrial Digital Twins; Market Size And Forecast: Digital Twins For Industrial Facilities 2021-2026 Global
Discover more Asset Maintenance Software & Services content
See More
About The Author
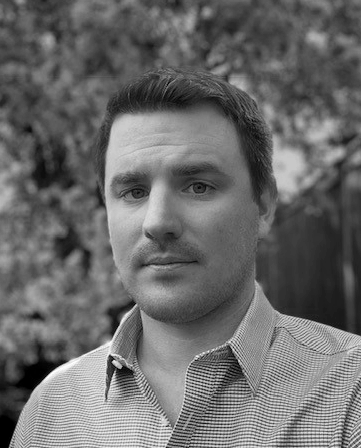
Joseph O'Brien
Senior Industry