Apple’s Latest Right To Repair Decision Could Signal A New Era Of Remanufacturing And Circularity
The right to repair movement has been picking up speed across the US and EU, with the EU having welcomed provisional agreements on the Right to Repair Directive (R2RD) in February. As of March 27th, meanwhile, five US states have passed legislation targeting digital electronic equipment, farm equipment and appliances. The latest, Oregon Senate Bill 1596, introduced new implications for manufacturers with a ban on parts pairing – a method of using software to identify components through unique identifiers and restricting repairs that use non-conforming components. In response to these additional repair requirements, Apple announced on April 11th that it will now allow the utilization of used components for iPhone repairs, driving increased component reuse and circularity.
Although current right to repair legislation targets reuse and repair, the EU’s expansion of extended producer responsibility (EPR) regulations – which make original equipment manufacturers (OEMs) responsible for the full life cycle of their products through to disposal – into new industries could trigger the adoption of additional circularity models. With potential for revenue decreases due to right to repair legislation and increased costs associated with EPR-related recycling and disposal, OEMs may soon look to remanufacture and refurbish their own products to capitalize on new circular economy markets and generate new revenues. Depending on customers’ quality and warranty demands (see below), manufacturers can provide them with more cost-effective (compared to new) and higher quality (compared to used) components for repair and end-of-life replacement. As manufacturers face new regulations and shifting customer sentiment, they may soon:
- Leverage remanufacturing to reduce customers’ total cost of ownership.
OEMs can gain a competitive advantage in the secondhand market and boost revenues by offering programmes focused on asset replacement and repair. These initiatives can leverage remanufacturing to provide lower-cost products with warranties and quality equivalent to new products.
- Improve design for repairability to enable more efficient remanufacturing.
Many organizations are already investing in sustainable product design, enabling highly efficient disassembly processes, making refurbishment and remanufacturing inherently more efficient. Respondents to the Verdantix Global Corporate Survey 2023: ESG & Sustainability Budgets, Priorities And Tech Preferences recognize the importance of this: 38% of firms expect to increase investment in product stewardship and sustainable product design software applications in 2024 compared with 2023.
- Store asset lifecycle data to provide secondary owners more transparency.
Digital product passports (DPPs) allow businesses to collect and share information from throughout a product’s life cycle, enabling consumers make more informed buying decisions. Apple’s announcement also highlighted a change to its internal DPP technology, enabling second and third owners of an iPhone to see the entire repair history of the phone and if used components were installed. This allows customers to feel more comfortable in purchasing second-life components.
While circularity poses new challenges and risks for manufacturers, firms that adopt an integrated approach stand to benefit from new revenue streams, improved customer perception and a more sustainable business model.
For a deeper dive into the current state of remanufacturing and how industries are leveraging it, read Verdantix Strategic Focus: Redefining The Role Of Remanufacturing In The Circular Economy Through Innovation.
About The Author
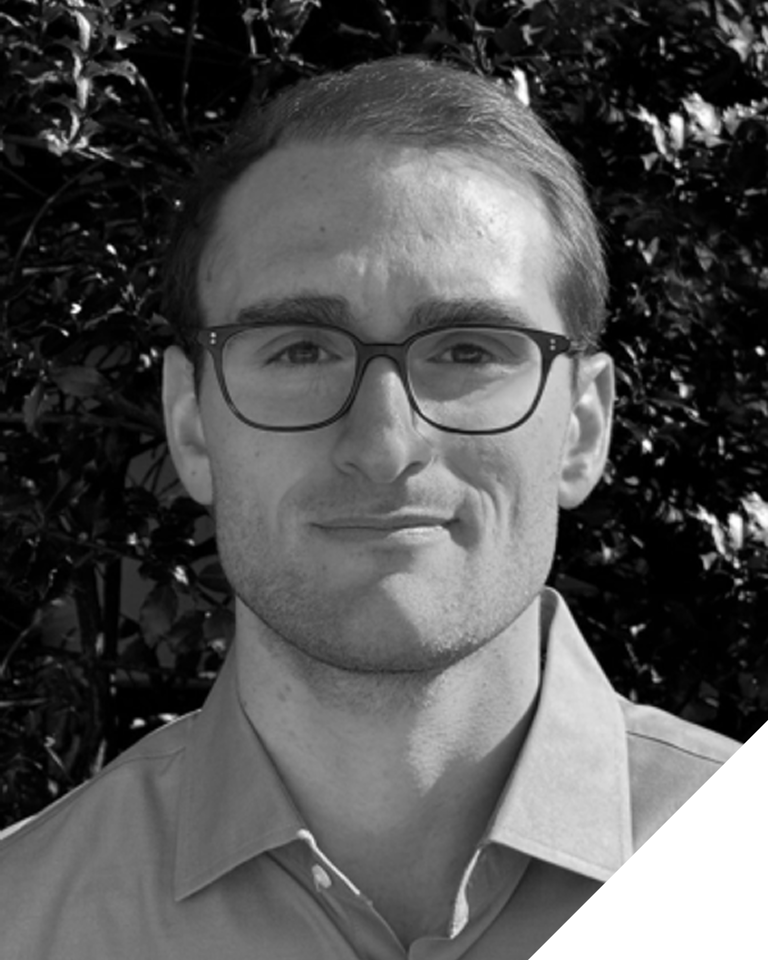
Josh Graessle
Senior Analyst