Reducing Lost Time Injury Frequency Rates (LTIFR) With EHS Digital Technology
Lost time injuries (LTI) are incidents resulting in injuries that prevent a worker from performing their duties or missing work. The higher its frequency rate (FR), the greater an indication that there are gaps in a firm’s EHS programme. Higher LTIFR will mean lower productivity and higher insurance premiums. According to the Health and Safety Executive (HSE), the UK experienced 4.7 million working days lost due to non-fatal workplace injuries in the period of 2018 to 2019. Additionally, the annual cost of workplace injuries as measured by the HSE during the period from 2017 to 2018 was £5.2 billion. Hence, LTIs are detrimental to the financial performance of firms and the economy as a whole. Firms also have a moral obligation to ensure the safety of their workers.
The HSE estimated that from the 2018 to 2019 injury rates, slips, trips, falls and lifting or carrying accounted for more than 20% of injuries. Striking from moving objects, acts of violence and falls from height accounted for approximately 10% of injuries. Each of these incidents were sources of LTIs, but what are the contributing factors to these types of injuries? Injuries can arise from a variety of factors including inadequate training, poor control of work activities, poor contractor management and a lack of hazard visibility.
EHS technology, as a whole, offers a range of practical methods for controlling sources and causes of LTIs (see Verdantix Strategic Focus: Incorporating Technology Into The Hierarchy Of Controls). Typical examples include wearable sensors for proximity detection and training software solutions offered via mobile apps. Training software solutions from the likes of KPA, Intelex, and Gensuite are administrative controls that firms use to manage systemic risks - risks contributing to injuries but are not direct causes. Similarly, control of work solutions and wearable sensors enhance the visibility of immediate risks to health (see Verdantix New Approaches To Reducing Serious Injuries, Fatalities And High Potential Events). For instance, Merck applied Axonify’s AI-powered microlearning platform to reduce LTIFR by 50% across its sites in comparison to 2014 levels (see Verdantix Merck Sharp & Dohme Drives Strong Safety Culture Engagement Through Safety Training Software). Furthermore, Chevron used wearable and IoT sensors to enhance hazard visibility across crane lifting operations, resulting in increased productivity and reduced incident response times (see Verdantix Chevron Partners With Accenture To Reduce Crane-Related Industrial Accidents Via Proximity Sensors And Analytics). These examples help showcase how the practical applications of EHS digital technology can aid in reducing firms' LTIFRs.
About The Author
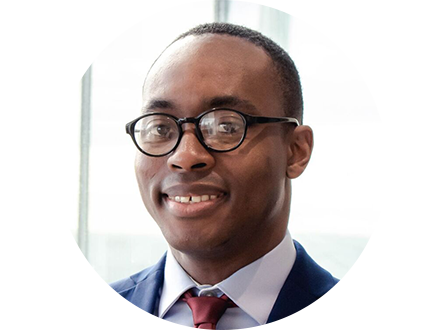
Kel Udeala
Industry Analyst