Flutura Delivers Scalable Digital Twins For Industrial Use Cases
Over the last decade the amount of data created has rapidly increased. According to IDC, the amount of data created doubles every 18-months to two years. This abundance of data does not always translate into business benefits. A survey conducted by PwC, a professional services provider, and Iron Mountain, an energy storage specialist, of 1,800 senior executives in North America and Europe, found that 43% of respondents derived little tangible benefit from information, while 23% derived no benefit whatsoever. This gulf between collection and utilisation creates a major business challenge for the ongoing success of the IoT market. Flutura, an industrial IoT platform provider, delivers a solution for this challenge.
Flutura’s offering, Cerebra, leverages disparate data flows from an industrial facility to improve asset uptime and operational efficiency. Flutura was founded in 2012 and is headquartered in Houston, Texas, USA with over 120 employees based in the US and in India. Flutura boasts a plethora of large global clients such as ABB, Honeywell, Shell, and TechnipFMC. In 2017, Shell selected Flutura, along with a group of other vendors, to deliver Cerebra for the former’s iShale multi-well pad and production facility in East Slash Range development area of the Permian Basin in West Texas. The iShale development leveraged automation, digitization and analytics to reduce the industrial intensity of shale development. The project achieved a 20% reduction in well pad implementation costs, with 40% reduction of in-field construction costs and 50% less health and safety construction exposure hours compared with traditional pads.
Flutura leverages data streams from connected assets, operational data, and IT information to deliver business benefits through digital twins at three levels of granularity. The first level twin creates a simulation of an individual piece of equipment through physics-based models and leveraging subsystems data. Benefits derived from this type of twin include increased uptime and improved equipment efficiency. The second level twin simulates facility level processes, bringing in data from equipment along with asset management data on the processes involved. These digital twins provide improvements in throughput, output, and consumables. The third and highest-level twin brings together multiple process twins to create a single system twin of the whole industrial facility. This top-level twin creates improvements in both quality and yield by predicting and simulating operations to identify bottlenecks and quality challenges. These three twins enable firms to take advantage of data that previously sat dormant to create new business values.
For more information on digital twins, register for the Verdantix webinar: Digital Twins For Industrial Facilities: Key Trends And Market Forecast 2020 - 2040
About The Author
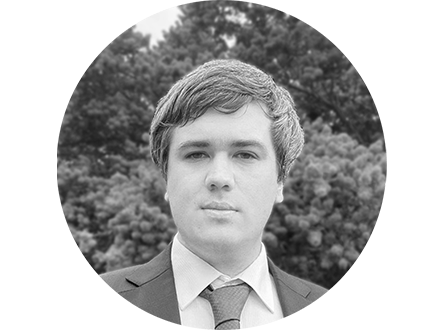
Sebastian Winter
Industry Analyst